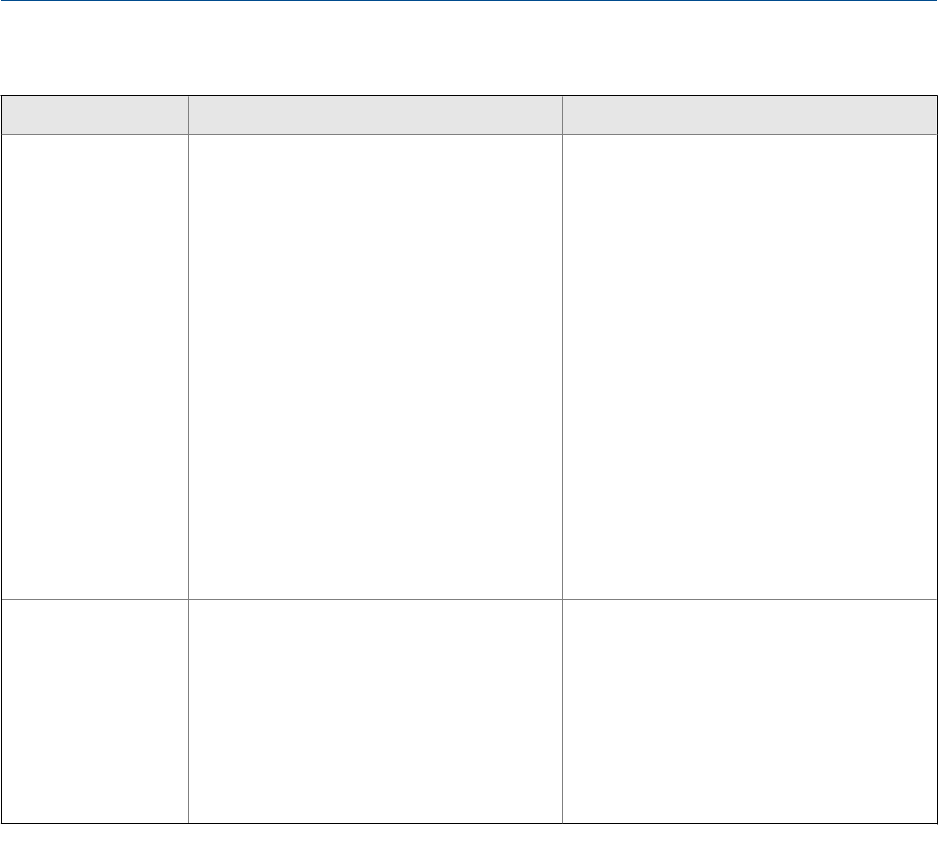
Viscosity measurement problems and recommended actions (continued)Table 10-2:
Problem Possible causes Recommended actions
Viscosity reading inac-
curate
• Incorrect calibration factors
• Inappropriate viscosity offset or viscosity
meter factor
• Flow rate too low or too high
• Bypass not fully closed
• Deposition or coating, especially asphal-
tenes, on the tines
• Fork laminate damaged
• Defective thermal insulation
• Boundary effect
• Verify the calibration factors. Ensure that
the viscosity ranges are appropriate for
your process fluid.
• Adjust the viscosity offset or viscosity me-
ter factor.
• Adjust the flow rate or the diameter of the
flow-through chamber. Refer to the instal-
lation manual for flow requirements and
best practices.
• Ensure that the installation type matches
the calibration. Refer to the installation
manual.
• Close the bypass.
• Clean the tines.
• Check for physical damage to the tines or
laminate.
• Repair or replace the thermal insulation.
• Check the pump delivery and service the
pump as required.
Referred viscosity
reading inaccurate
• Inaccurate line viscosity measurement
• Inaccurate line temperature measurement
• Incorrect referred viscosity configuration
• Inaccurate measurement of laboratory
sample
• Ensure that line viscosity measurement is
as accurate as possible.
• Ensure that the temperature value used in
referred viscosity measurement is as accu-
rate as possible.
• Verify the configuration of referred viscosi-
ty measurement.
• Repeat the laboratory measurement, en-
suring that reference conditions match.
Troubleshooting
Configuration and Use Manual 173