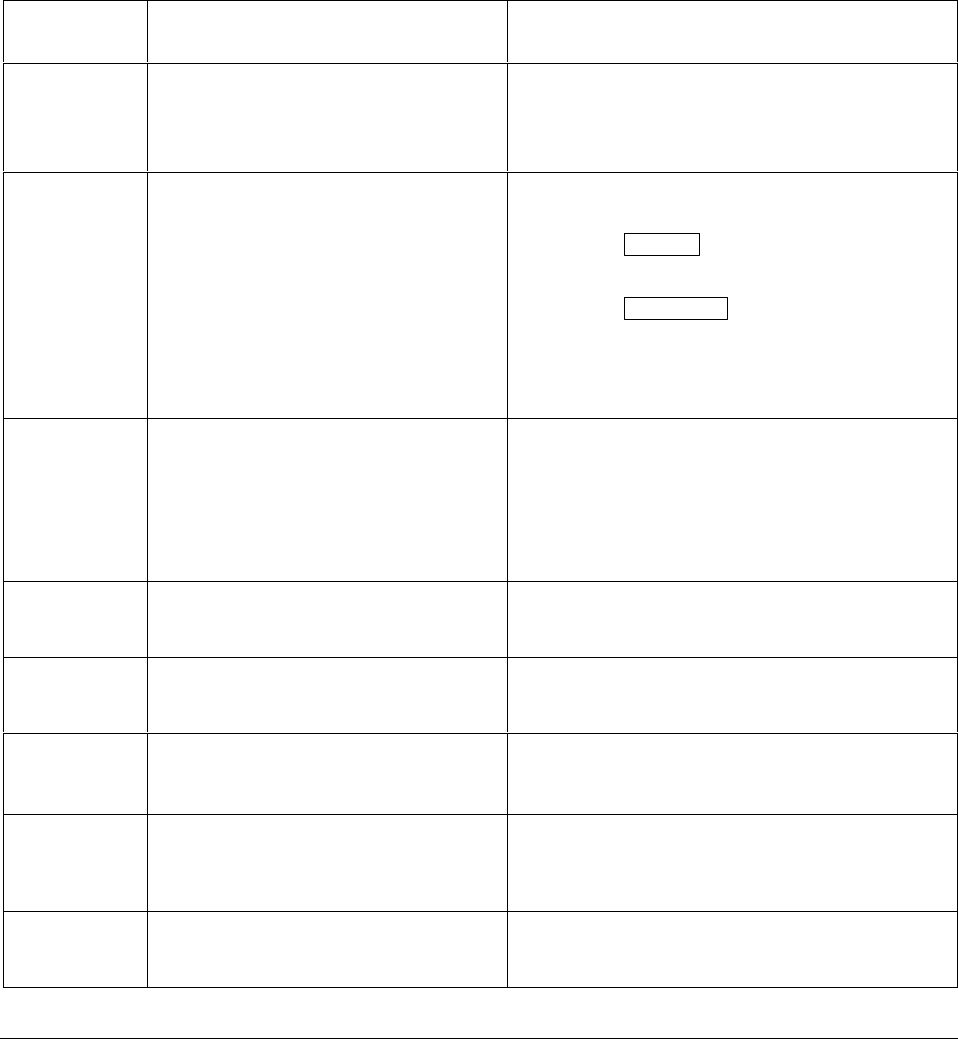
250 UDC 3300 Controller Product Manual 4/00
9.5 Background Tests
Introduction
The UDC 3300 performs on-going background tests to verify data and
memory integrity. If there is a malfunction, an error message will be
displayed (blinking) in the lower display.
Background tests
In the case of more than one simultaneous malfunction, only the one with
the highest priority will appear in the lower display. Table 9-6 lists these
background tests, the reason for their failure, and how to correct the
problem.
Table 9-6 Background Tests
Lower
Display
Reason for Failure How to Correct the Problem
EE FAIL
Unable to write to non-volatile memory.
Anytime you change a parameter and it is
not accepted, you will see EE FAIL.
1. Check the accuracy of the parameter and re-enter.
2. Try to change something in configuration.
3. Run through STATUS tests to re-write to
EEPROM.
FAILSAFE
or
FAILSF2
(Loop 2)
This error message shows whenever the
controller goes into a failsafe mode of
operation. This will happen if:
• RAM test failed
• Configuration test failed
• Calibration test failed
• Burnout configured for none and
the input failed.
1. Run through STATUS check to determine the
reason for the failure.
2. Press the SET UP
key until STATUS appears in
the lower display.
3. Press the FUNCTION key to see what tests
pass or fail, then run through the STATUS codes a
second time to see if the error cleared.
Correct according to the recommendations given
in Table 9-5.
INP1FAIL
Two consecutive failures of input 1
integration. i.e., cannot make analog to
digital conversion. This will happen if:
• Upscale or Downscale burnout is
selected
• Input not configured correctly
1. Make sure the actuation is configured correctly.
See Section 3 - Configuration.
2. Make sure the input is correct.
3. Check for gross over-ranging.
4. Replace factory calibration. See Section 7.6.
5. Replace the cold junction assembly.
INP2FAIL
Two consecutive failures of input 2
integration. i.e., cannot make analog to
digital conversion.
Same as INP1FAIL above.
INP3FAIL
Two consecutive failures of input 3
integration, i.e., cannot make analog to
digital conversion.
Same as INP1FAIL above.
SW FAIL
Position Proportional input slidewire failure 1. Check motor slidewire connections.
2. Recalibrate the slidewire motor position. see the
calibration section (Section 8.3).
CAL MTR
Position Proportional or 3 Position Step
Control with Motor Position Indication,
Auto Cal never performed.
1. Calibrate the controller for Position Proportional
output. Refer to Subsection 8.3 – Position
Proportional and 3 Position Step Output
Calibration.
CONF ERR
• PV low limit is > PV high limit
• SP low limit is > SP high limit
• Output low limit > Output high limit
1. Check the configuration for each item and
reconfigure if necessary.