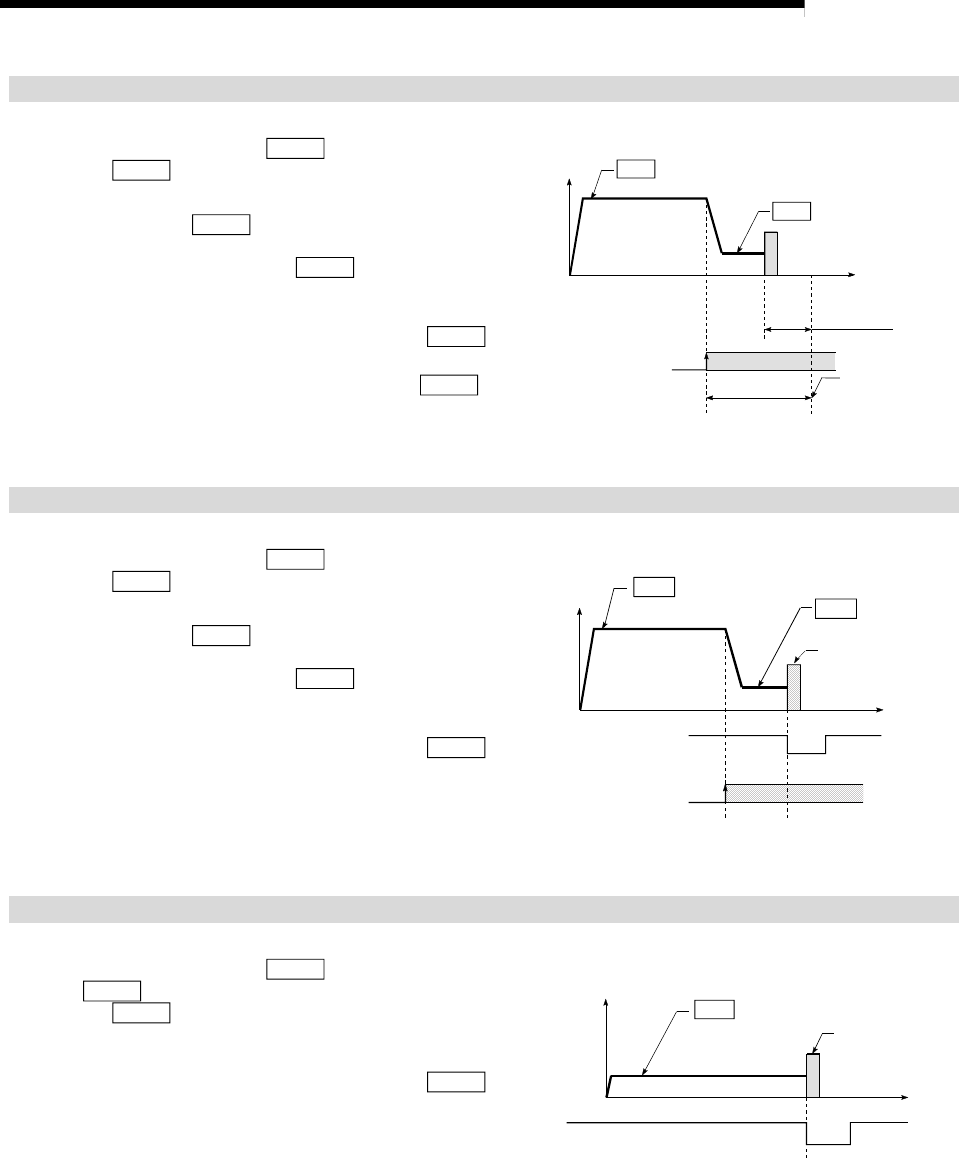
5 - 46
MELSEC-
A
5 DATA USED FOR POSITIONING CONTROL
1 : Stopper stop method 1)
(1) Start machine zero point return.
(Start movement at the "
Pr.48
Zero point return speed" in
the "
Pr.46
Zero point return direction".)
(2) Detect the near-point dog ON, and start deceleration.
(3) Decelerate to "
Pr.49
Creep speed", and move with the
creep speed.
(At this time, setting for the "
Pr.56
Zero point return torque
limit value" is required. If the torque is not limited, the
servomotor could be damaged in step (4).)
(4) The axis contacts against the stopper at the "
Pr.49
Creep
speed", and then stops.
(5) When the near-point dog turns ON and the"
Pr.51
Zero
point return dwell time" is passed, the pulse output from the
D75P2 stops, and the machine zero point return is
completed.
t
V
(1)
(2)
(3) (4)
(5)
Near-point dog OFF
Zero point return speed
Pr.48
Creep speed
Pr.49
Range to forcibly stop
the servomotor
rotation with the stopper.
Dwell time counting
Dwell time up
ON
2 : Stopper stop method 2)
(1) Start machine zero point return.
(Start movement at the "
Pr.48
Zero point return speed" in
the "
Pr.46
Zero point return direction".)
(2) Detect the near-point dog ON, and start deceleration.
(3) Decelerate to "
Pr.49
Creep speed", and move with the
creep speed.
(At this time, setting for the "
Pr.56
Zero point return torque
limit value" is required. If the torque is not limited, the
servomotor could be damaged in step (4).)
(4) The axis contacts against the stopper at the "
Pr.49
Creep
speed", and then stops.
(5) After stopping, the pulse output from the D75P2 stops with
the zero point signal (a signal issued from an external
device upon detection of contact with the stopper), and the
machine zero point return is completed.
t
V
ON
(1)
(2)
(3) (4)
(5)
Near-point dog
Zero point signal
Zero point return speed
Pr.48
Pr.49
Creep speed
Stop with stopper
OFF
3 : Stopper stop method 3)
(1) Start machine zero point return.
(Start movement at the "
Pr.49
Creep speed" in the
"
Pr.46
Zero point return direction". At this time, setting for
the "
Pr.56
Zero point return torque limit value" is required.
If the torque is not limited, the servomotor could be
damaged in step (2).)
(2) The axis contacts against the stopper at the "
Pr.49
Creep
speed", and then stops.
(3) After stopping, the pulse output from the D75P2 stops with
the zero point signal (a signal issued from an external
device upon detection of contact with the stopper), and the
machine zero point return is completed.
t
V
(1)
(2)
(3)
Zero point signal
Creep speed
Pr.49
Stop with stoppe
r