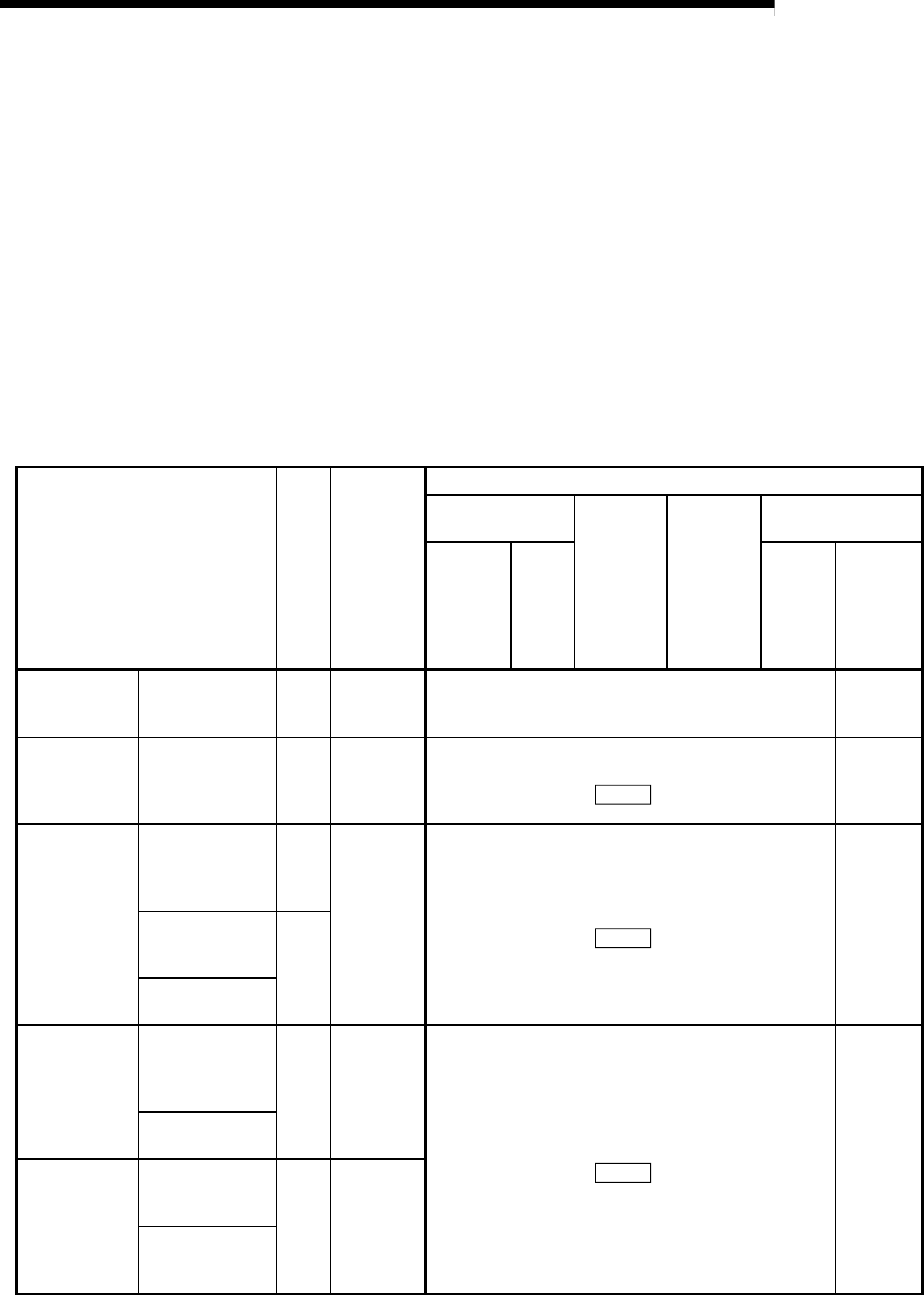
1 - 16
MELSEC-
A
1 PRODUCT OUTLINE
1.2.3 Outline of stopping
Each control is stopped in the following cases.
(1) When each control is completed normally.
(2) When the drive unit READY signal is turned OFF.
(3) When the data link of CC-Link stops.
(4) When Initial data setting request (RY(n+7)9) turns ON and Remote station READY
(RX(n+7)B) turns OFF.
(5) When an error occurs in the D75P2.
(6) When control is intentionally stopped (Stop signal from master module turned ON,
stop from peripheral device, etc.)
The outline for the stopping process in these cases is shown below. (Excluding (1) for
normal stopping.)
Stop cause
Stop
axis
Axis
operation
status after
stopping
(RWrn+7,
RWrn+15)
Stop process
Zero point return
control
Main
positioning
control
Advanced
positioning
control
Manual control
Machine
zero point
return
control
High-
speed
zero
point
return
control
JOG
opera-
tion
Manual
pulse
generator
operation
Forced stop
Drive unit
READY signal
OFF
Each
axis
During
error
Immediate stop
Immediate
stop
Fatal stop
(Stop group 1)
Hardware stroke
limit upper/lower
limit error
occurrence
Each
axis
During
error
Deceleration stop/sudden stop
(Select with Pr.38 )
Decelera-
tion stop
Emergency
stop
(Stop group 2)
Software stroke
limit upper/lower
limit error
occurrence
Each
axis
During
error
Deceleration stop/sudden stop
(Select with
Pr.39 )
Decelera-
tion stop
Remote station
READY signal
OFF
All
axes
"Stop" input from
peripheral device
Relatively safe
stop
(Stop group 3)
Axis error
detection (Error
other than stop
group 1 or 2)
Each
axis
During
error
Deceleration stop/sudden stop
(Select with
Pr.40 )
Decelera-
tion stop
Error in test
mode
Intentional stop
(Stop group 3)
"Stop signal" ON
from external
source
Each
axis
When
stopped
(While
waiting)
"Axis stop signal"
ON from PLC
CPU